No introduction is needed for J. Lohr Vineyards & Wines. If you ever tasted wine from Paso Robles, there is a good chance it was crafted by the J. Lohr team with grapes from their estate vineyards.
BarrelWise is excited to tell this story at the 6-month mark of J. Lohr implementing our technology. It is intriguing how a winery with long-standing protocols can manage to be an early adopter of technology, especially when it requires new ways of thinking and operating.
This round, we sat down with Brett Vassar from J. Lohr’s red wine team to hear more about his firsthand experience implementing the BarrelWise FS1 System. Brett has been with J. Lohr for 7 years, started as a Lab Technician, and is now Assistant Winemaker for their red wine programs.
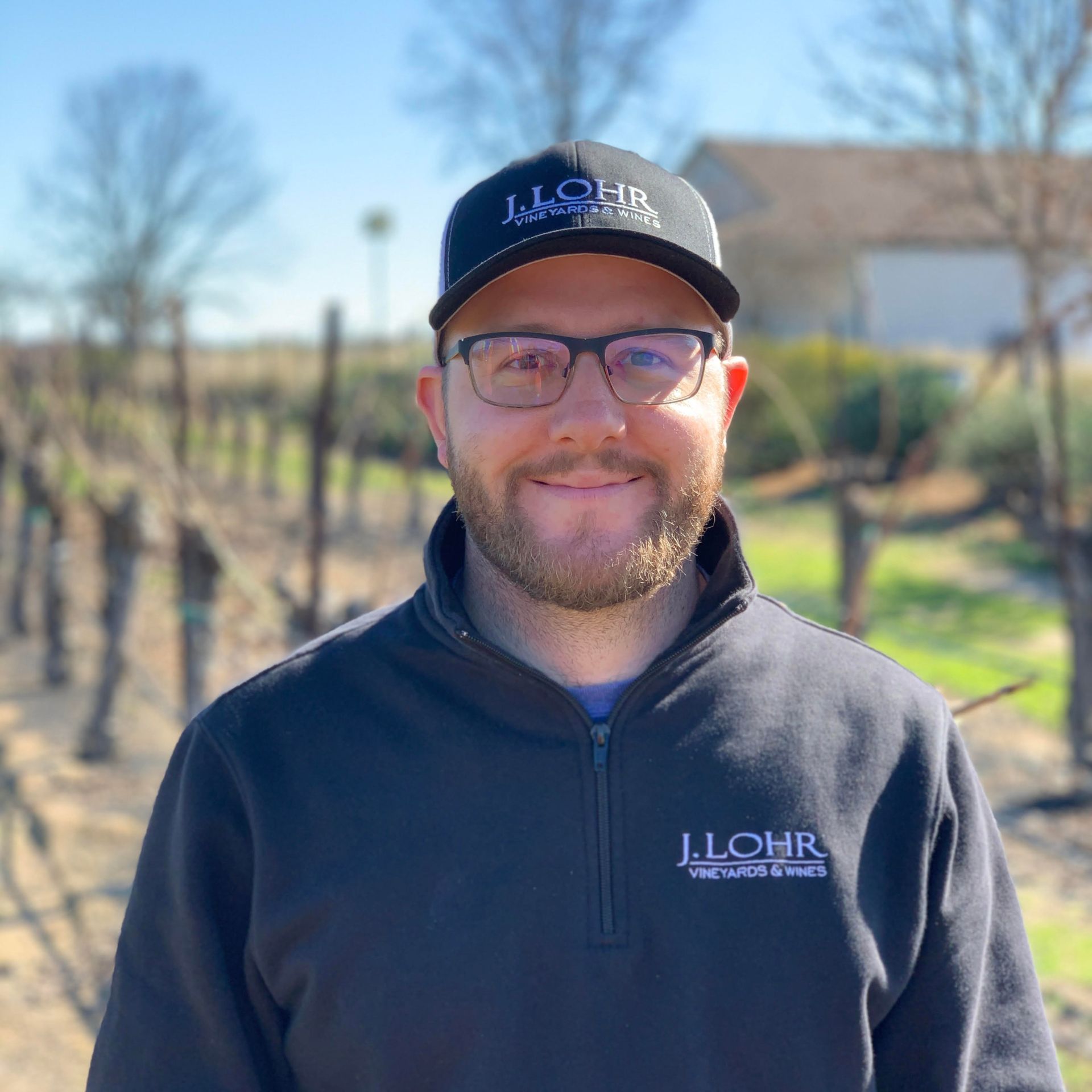
J. Lohr & BarrelWise: A story that began with “Why not”
In early 2022, J. Lohr's winemaking team was having a conversation about researching useful parameters to manage in barrel-aged wine when theBarrelWise FS1 came up.
“Why not? Let’s look into it”, Brett recalled his discussion with Steve (Steve Peck – J. Lohr’s VP of Winemaking), “Could this tool be useful for the number of barrels we have?”.
A demo session was arranged in the summer at their Paso Robles facility, with winemaking and cellar teams coming together to assess the tool. The team went over how the unit works, measured free SO2 in their own barrels, let the barrel room team try it out, and looked at the results streaming back to the winemaker's portal.
Before the 2022 harvest, J. Lohr signed to implement the FS1 System, with the first unit set to be deployed in early 2023.
“Do you want to spend an hour writing sample labels, or do you want to spend an hour improving the quality of the wine?”
There are many set-in-stone protocols that the J. Lohr team has developed over the years to uphold their unquestioned wine quality. Managing free SO₂ levels is essential to preventing Brettanomyces outbreaks for example.
“So how can we work through this, to evolve and make this technology part of our workflow?” Brett explained the process, “There is compliance, work orders, lab, barrel room, and making sure the results get to the winemaking team. All have to be figured out so the FS1 works in our workflow. For example, the way we do topping for SO2 is samples being brought to the lab, who has control of the analysis. But now that the cellar has control of the analysis where the samples were pulled and processed completely there, how can we still get pH, VA, and all those other basic analyses the lab normally runs without having lab samples like before? We have to think through and modify our SOPs and protocols.”
It takes time and effort to implement new technology — some might say it is a daunting task to get people on board to change their normal routine — so, what was J. Lohr's motivation?
“The biggest thing we saw is that the FS1 allows us to get rid of the mundane work — sampling time, writing sample labels, cleaning sample tubes, all things that consume time, and allow people to do other things.” Brett pointed out. “It comes down to: do you want to spend an hour writing sample labels, or do you want to spend an hour improving the quality of the wine?”
That was a nice sum-up. A clear and concise notion to guide the effort during times of change.
“Getting more efficient was the big thing. It alleviates a bit of work to be handled in the lab and allows us to work with new projects and new equipment that improve the quality of the wine. Two biggest things for J. Lohr so far, efficiency and quality.” he told the BarrelWise team.
All hands on deck, eyes on the prize, and keep pushing forward
What helped people step out of their long-standing routine and out of their comfort zone?
“Using the FS1, and repetition.” Brett reflected.
“Every time we hit a bottleneck, I looked at how we could rework, resample, things to do in order to hit the needs of all departments. We sat down with all departments to discuss how are we going to interact with the machine, what could be better, and how can we improve our workflow. It’s really just not giving up and keep reiterating the goal.”
It’s always easier to go back to the way it was, but with repetition and using the instrument, Brett saw people become more comfortable. “A week or so using it, the workflow became really easy.”
“For us, the thinking was more on how to still get the samples to the lab for pH, VA, and other parameters, instead of whether we should lose the benefits of the FS1 entirely,” Brett elaborated. “We knew what the FS1 can do and compared that to the previous topping method to figure out what the best way is to get samples to the lab to get other analyses done. So, it’s more about how do we fit this into our current methods and being smart about how to order the samples to leverage the technology as much as possible.”
The team now does post physical composite for the lab to check parameters like VA, pH after free SO2 checks. The barrel room team no longer has to pull the barrels down and wait for analysis results, then do topping. They can put the barrels away immediately, and the lab can process the samples for other routine analyses and update the database when they get to it.
“We keep our focus on the overall J. Lohr time instead of the individual team time. We understand this isn’t about shifting the lab time and putting it to the cellar, but instead, with the same J. Lohr’s number of hours, we can now achieve so much more.” Brett stated.
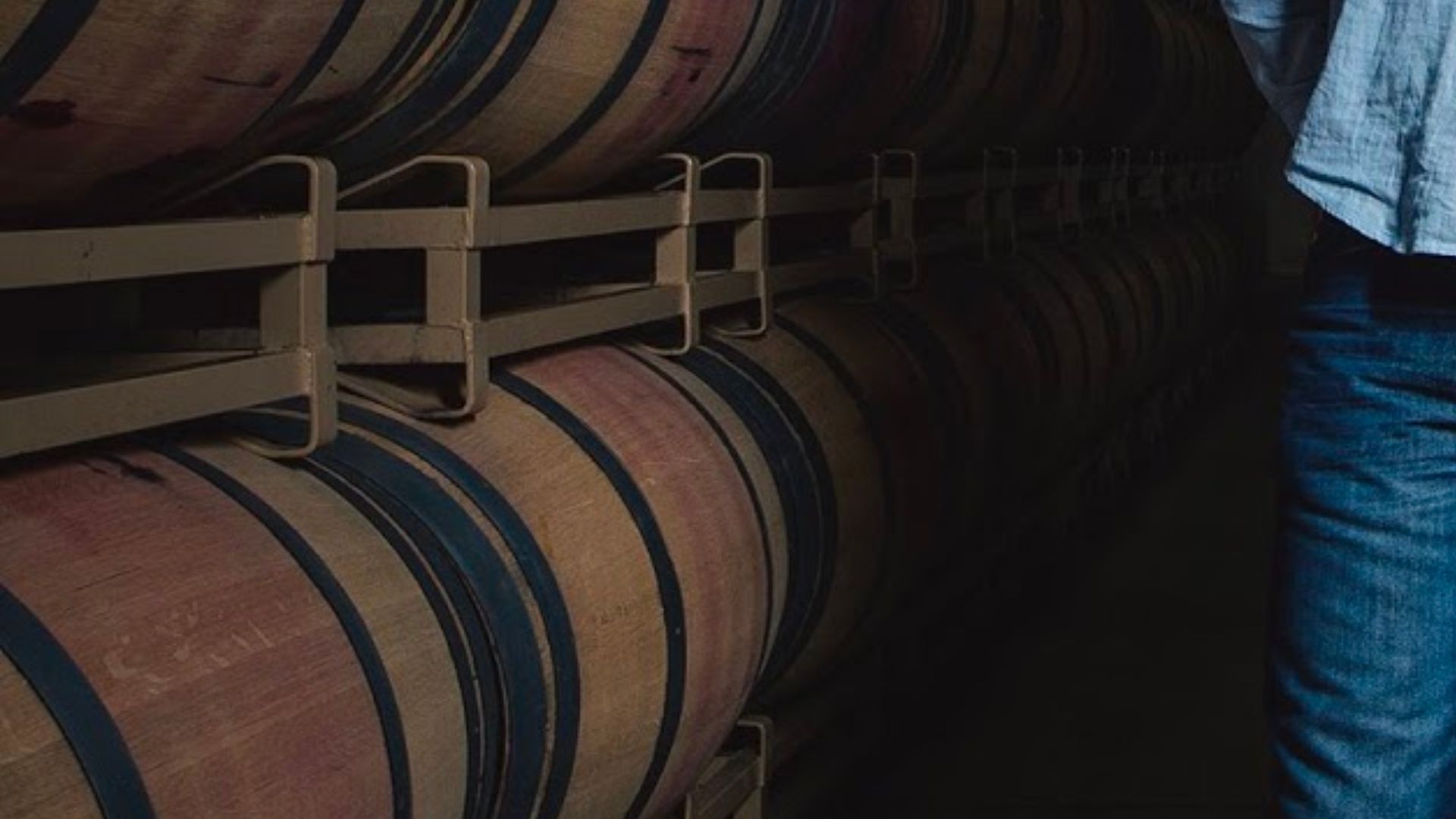
Gaining momentum with exciting time ahead
J. Lohr is currently running 50+ samples a day on the FS1, and it’s still early days.
The FS1 usage, as we write, is full steam ahead for J. Lohr’s Seven Oaks Cabernet Sauvignon, and Los Osos Merlot programs. Brett developed a topping report so winemakers could have data for the day and have their eyes on it.
“With the FS1, the data collection is so efficient that scaling up SO2 sampling no longer prompts the challenge of how to balance it with other lab priorities. Doing our due diligence became a lot easier.” Brett explained the current state. He has also adopted the dynamic sampling protocol to further balance efficiency and visibility.
Folks in the cellar are now comfortable using the FS1. The number of operators is growing and it has been very simple to train new people.
Brett could also know if it’s a new person using the machine just by looking at the results in the portal. “If the person wasn’t running the first sample twice after water, I could tell they’re new because those who used it before will run the first sample twice to clear the water”. Don’t we all love these data nuggets that give us the vision as if we were there when it happened.
Smoothing the adoption process with proactive and instant customer support
Great customer support makes it easier to establish new routine and keep it up.
“One thing I've been impressed with is the customer service. I’ll get a message from BarrelWise at six or seven in the morning and I just have to copy your message to the cellar who’ve been running SO2 at 5:30am” he said.
“The quick response from BarrelWise every time an issue happened, and sometimes even before we noticed, just helped move it forward and prevent us from falling back to the old SOPs.”
Brett also found it helpful that BarrelWise acts on what needs to be adjusted in the product. “You guys always come in with “how can we help make your protocols be more efficient”. When we have a wish list — having the app in Spanish, easily exporting data, and more — you find a way to support our needs and make it happen.”
In fact, a week after this interview with Brett, we launched the in-app customer support chat that made communication between BarrelWise support team and FS1 operators even more immediate and convenient. Another item on Brett's wish list came true.
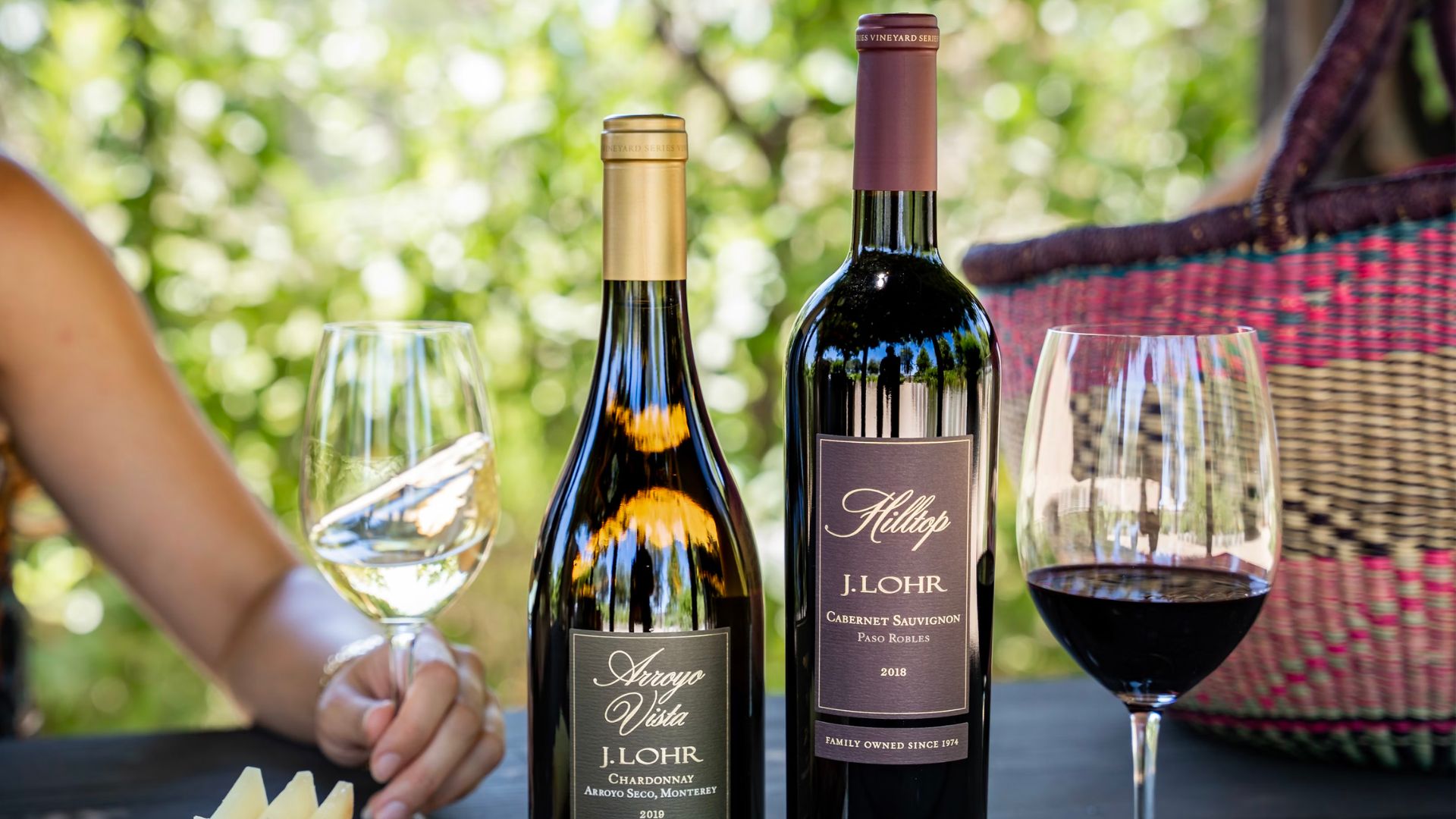
On the forefront of technology, leading by example
“J. Lohr is a big proponent of new technology and we do so by being early adopters. We want to be at the forefront, and we’re not afraid to try things out.” Brett firmly said, “It’s also great to work in a place where technology is leveraged to improve efficiency.”
They were among the earliest customers of BarrelWise.
Brett recalled a talk with Steve Peck about how measuring dissolved oxygen used to be done in the lab with a time-consuming and finicky process; then, 15-20 years ago, dissolved oxygen meters arrived and changed the scene.“BarrelWise is doing the same thing for SO2. It turns a lab-centric process into something the cellar can do as part of their day-to-day operations.”
We did, with a more elaborated data management infrastructure, so everyone is connected to a single source of truth for the analysis results.
Bonus part: Brett’s Favorites
Brett’s favorite thing about FS1 is being able to calibrate the machine to emulate the results that he is getting on the lab equipment, used as a primary reference. “You can’t get this with other SO2 testing methods. For the FS1, we sample a few barrels and run it side-by-side with our primary reference to calibrate the unit; and usually, we can nail it within 2-3ppm, which is very good for SO2 numbers using separate instruments.”